ICTM Conference: Turbine Construction between Big Data and Additive Manufacturing
The ICTM Conference has established itself as a networking hub for the international turbomachinery industry. For the fourth time in a row, this biennial event was organized by the International Center for Turbomachinery Manufacturing ICTM in Aachen and in collaboration with the Fraunhofer Institutes for Production Technology IPT and Laser Technology ILT. This year’s conference took place February 15-16, 2017. More than 250 experts from 19 countries discussed how to more efficiently develop and manufacture turbines for power plants and aircraft in the digital age.
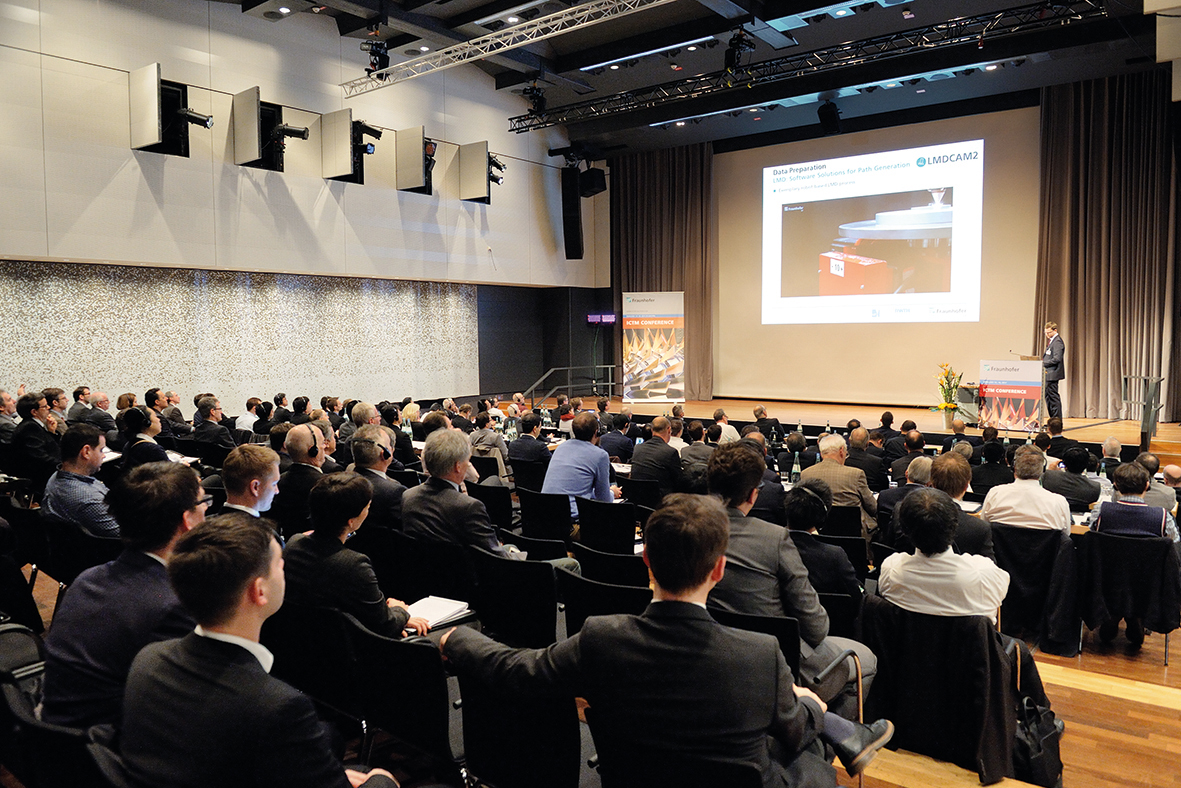
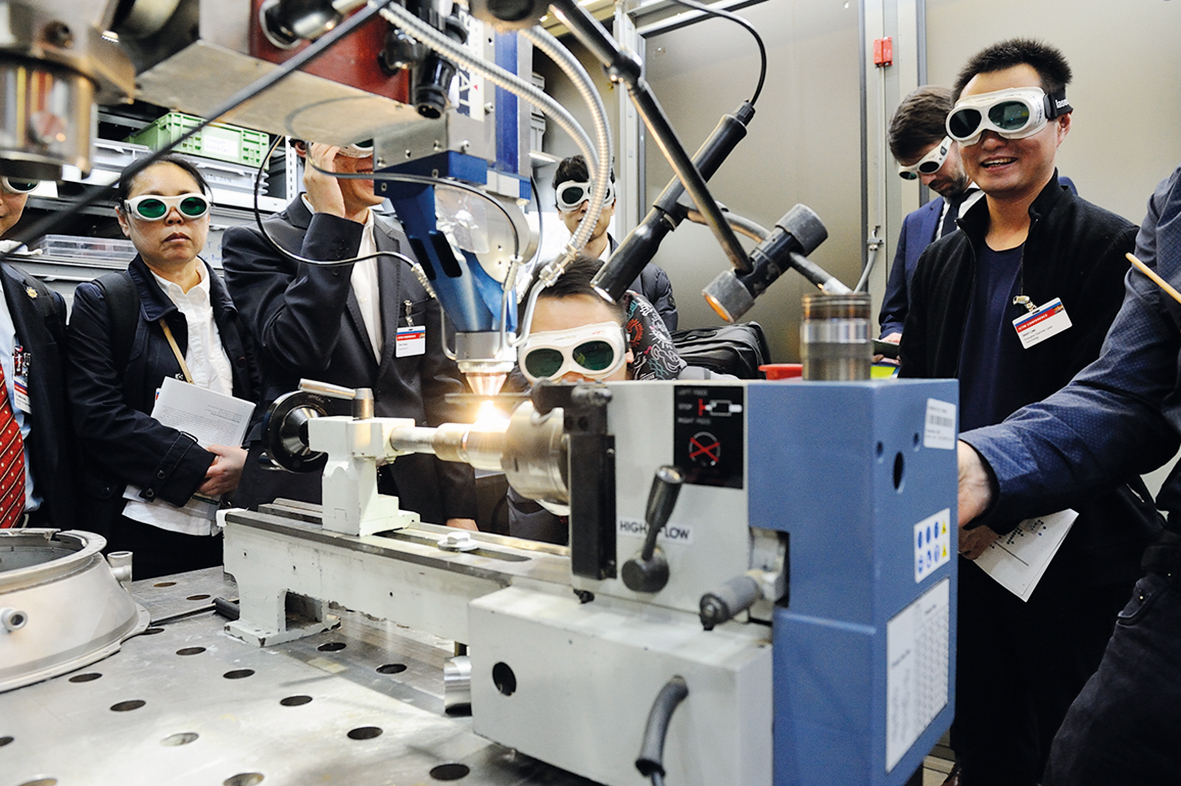
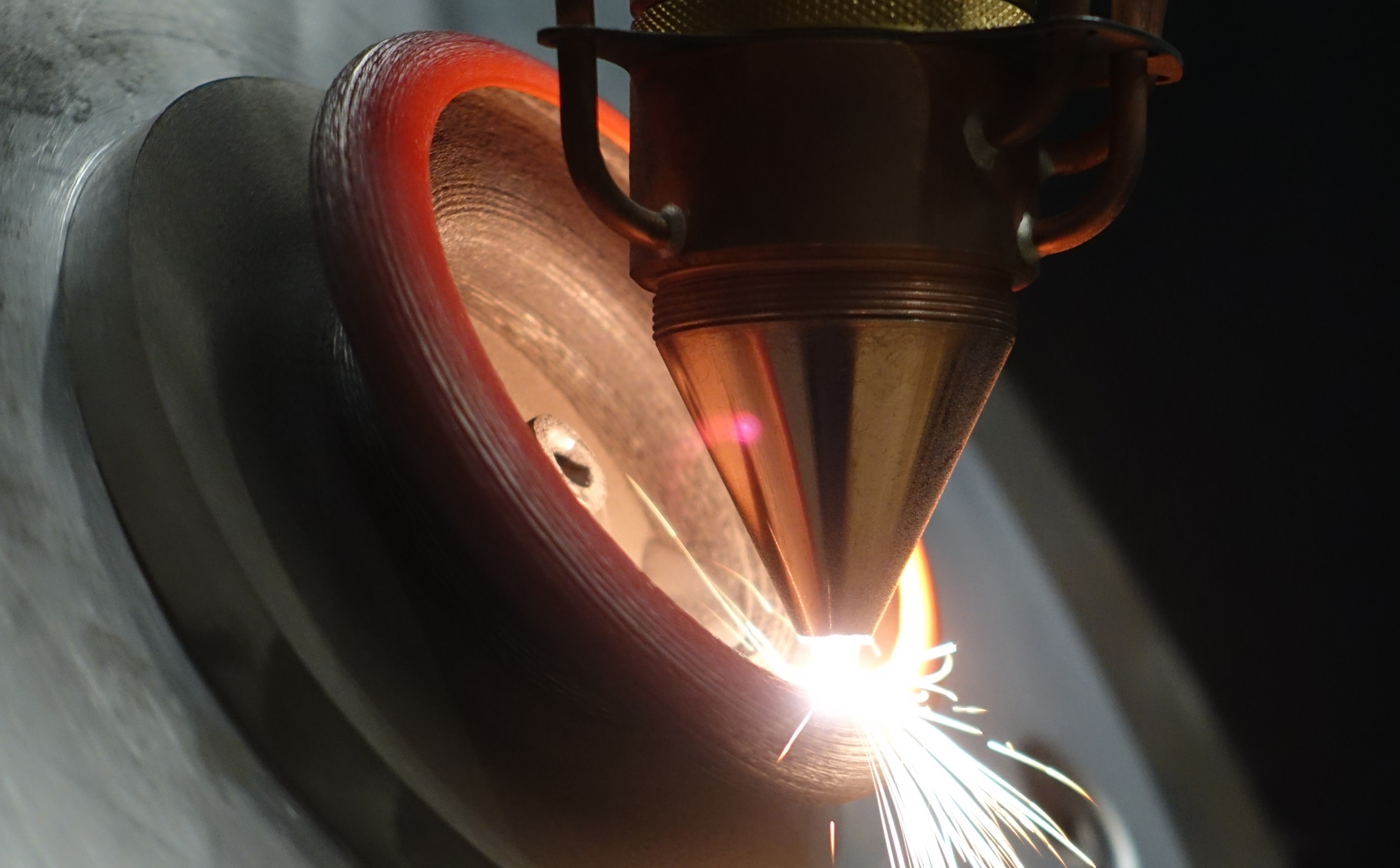
Over the two-day event, 21 presentations dealt with the influence of advanced machining, additive manufacturing and industry 4.0 on the production of turbomachinery. Turbine manufacturers, corporations and medium-sized companies representing key aspects of diverse process chains have met up every two years since 2011 at the popular conference in Aachen. The number of participants has also risen since the first ICTM Conference – from 190 to 250 – and the number of industry partners exhibiting their products has gone up from 10 to 15. It is particularly notable that the number of demonstrations put on by the two Fraunhofer Institutes has more than doubled. Whereas in 2011 there were 19 live demonstrations, by 2017 this number had risen to 44 – including demonstrations of additive manufacturing, ultrashort pulse lasers, 5-axis waterjet cutting, and cryogenic cooling of materials that are difficult to machine.
ICTM Center fosters Turbomachinery Expertise
Turbomachinery manufacturers have a great need to exchange information. Yet despite rapid access to information, it is becoming increasingly difficult to find the right facts and figures. "Going forward, you need to know where expertise in new technologies is being developed,” said Prof. Johannes Henrich Schleifenbaum, Head of Additive Manufacturing and Functional Layers at Fraunhofer ILT. However, to foster new developments, Schleifenbaum added that industry and research needed to work closely together in a targeted and coordinated way. Schleifenbaum, holder of the Chair for Digital Additive Production DAP at RWTH Aachen University, described the International Center for Turbomachinery Manufacturing ICTM, with its current tally of 30 partner companies, as a good example of collaboration in action in the field of turbomachinery production. Some of the multidisciplinary expertise developed there has already been made available to participants at this year’s ICTM Conference. “When you leave the conference, take this expertise away with you, so that you can draw inspiration from our ideas and innovations,” Schleifenbaum concluded. “Join the ICTM Center, collaborate with us, and become a part of this wonderful network!”
The founding members of the ICTM Center include Munich-based MTU Aero Engines, whose Chief Operating Officer Dr. Rainer Martens gave a presentation on digital engine production. The geared turbofan engines, in which MTU has a substantial stake, have become extremely popular in the aviation industry for reasons such as their low levels of fuel consumption, CO2 emissions and noise emissions. As a result, between 2009 and 2020, production of MTU’s components is expected to quadruple.
The Industrialization of Additive Manufacturing
At MTU, extremely complex and highly integrated compressor rotors play an important role. These compressor rotors have an innovative blade integrated disk (blisk) design and are constructed from heavy-duty titanium alloys that are characterized by their utmost precision (< 30 µm). To manufacture these blisks, MTU has spent over 70 million euros building a new production hall that features a high level of automation and digitalization. “Here we create a large quantity of big data, which we still have to convert to smart data that can then be of some benefit to us,” reported Dr. Martens in Aachen. “When it comes to turning centers, we are much more advanced because integrated measuring technology already allows us to compare data. For instance, we use geometric data to draw conclusions as to the condition of the machines.”
In addition, the company has been working extremely hard on new simulation techniques to improve production processes. The answer it has found is called integrated computational materials and manufacturing engineering (ICM²E). This new method for improving materials development and manufacturing links together results from individual simulations. The goal is to create a process that coordinates all the parameters so as to obtain a finished part that meets exact specifications.
How innovation changes in times of disruptive, revolutionary technologies that supersede other processes was a topic examined by Dr. Ingomar Kelbassa, Department Manager for Manufacturing Development and Industrialization at Siemens AG in Berlin (Power and Gas Division). “Additive manufacturing in conjunction with the digitalization of production allows us to significantly bypass traditional processes,” explained the former ILT researcher. "For that to happen, though, those involved have to change the way they think.” Recently, Siemens proved that using additive manufacturing as an alternative to standard approaches could pay off. The company had already introduced solutions for gas turbine combustion system components that were ready for production, but then it had a breakthrough in the 3D printing of rotating components. Siemens fully tested the turbine blades, which were produced from start to finish using additive manufacturing, in a gas turbine. The process employed the selective laser melting (SLM) process developed at Fraunhofer ILT. “The use of SLM leads to a paradigm shift in development and validation, enabling the innovation cycle to be shortened by up to 90 percent. The industrialization of additive manufacturing has thus begun,” Kelbassa explained.
Effectively Using the Advantages of Digital Transformation
The 18 presentations that followed were given by speakers from both industry and research, who examined further challenges facing today’s turbomachinery manufacturing. Among other issues, they considered developments in the fields of laser metal deposition and selective laser melting (Fraunhofer ILT), processes for blisk production (Fraunhofer IPT), and a newly developed method for analyzing big data in turbomachinery manufacturing (SAP). The growing number of sensors and powerful evaluation electronics brings about ever increasing amounts of data, known as “big data.” Here is a typical example: if a computer records 20 values (64 Bit) per millisecond, it will save 4.3 gigabytes of data over the course of an eight-hour shift. Yet how can we handle such a constantly growing volume of data? Which data can be processed in real time? How do users gather data from a wide range of sources? Every company must solve these and many other problems in the coming years if it wants to effectively use the advantages of digital transformation. As a result, big data is likely to be one of the main topics at the “5th Conference of the ICTM International Center for Turbomachinery Manufacturing Aachen” in February 2019.